For connecting two 12V batteries in parallel, the recommended wire gauge largely depends on the total current draw and the length of the wire. Typically, a wire gauge of 10 AWG is sufficient for most applications.
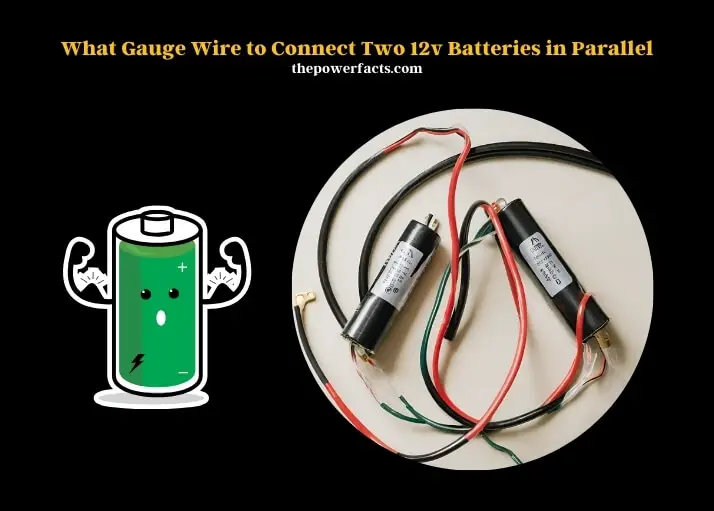
Connecting two 12V batteries in parallel is a common practice to increase capacity while maintaining the same voltage. This setup allows for extended usage time for devices and systems powered by these batteries. The key to a safe and efficient connection lies in choosing the correct wire gauge.
The wire must be capable of handling the combined current of both batteries without overheating or losing significant voltage. The choice of wire gauge affects not only the performance but also the safety of the electrical system. It’s essential to calculate the total expected current draw and consider the length of the wire run to determine the appropriate wire size.
Using a wire that is too thin can lead to excessive heat buildup, potentially causing wire damage or fire. On the other hand, a wire that is too thick might be unnecessarily expensive and difficult to work with.
In addition to selecting the right wire gauge, ensuring proper insulation and secure connections is crucial to prevent short circuits and ensure the longevity of the battery setup. This approach ensures that the system remains efficient, safe, and reliable over time, providing the desired power output without compromising on safety or performance.
Determining the Correct Wire Gauge for Parallel 12V Battery Connections
Choosing the right wire gauge is crucial for connecting two 12V batteries in parallel. This decision impacts not only the safety and efficiency of the battery system but also its overall performance. The wire gauge affects electrical resistance and current capacity, which in turn influences how well the system can distribute power without overheating.
Adhering to safety standards ensures that the setup remains secure under various conditions, while optimal heat dissipation helps in maintaining the longevity and reliability of the battery connection. Selecting an appropriate wire gauge requires a balance between these factors to achieve a setup that is both efficient and safe.
The Impact of Wire Length on Parallel Battery Configurations
The length of the wire connecting two 12V batteries in parallel plays a significant role in the system’s efficiency. A longer wire introduces more resistance, which can lead to a voltage drop across the connection. This reduction in voltage affects the system’s ability to deliver power effectively.
To maintain power efficiency, it’s essential to calculate the optimal wire length that minimizes resistance without compromising the flexibility or layout of the battery system. Understanding how voltage drop and resistance increase with wire length is key to optimizing the performance of parallel battery configurations.
Comparing Wire Materials for 12V Battery Systems
When connecting two 12V batteries in parallel, the choice of wire material is a critical consideration. Copper and aluminum are the most common materials, each with its advantages and disadvantages. Copper’s superior conductivity means it can carry more current with less resistance, leading to more efficient power transmission. However, it is also more expensive and heavier than aluminum.
Aluminum, on the other hand, offers a cost-effective alternative with decent conductivity and lighter weight, but it is more prone to corrosion and has a lower current capacity than copper. The decision between copper and aluminum wires depends on factors such as cost, weight, conductivity, and durability.
Calculating the Total Amperage in Parallel Battery Setups
In parallel battery configurations, calculating the total amperage is essential for selecting the correct wire gauge. The total current output is the sum of the individual batteries’ capacities, which dictates the wire’s required current capacity to safely handle the load.
This calculation influences the choice of wire gauge, as a wire that is too thin may overheat and fail, while a wire that is too thick could be unnecessarily expensive and cumbersome. The formula for total current and the capacities of each battery helps in making an informed decision on the wire gauge needed for a safe and efficient setup.
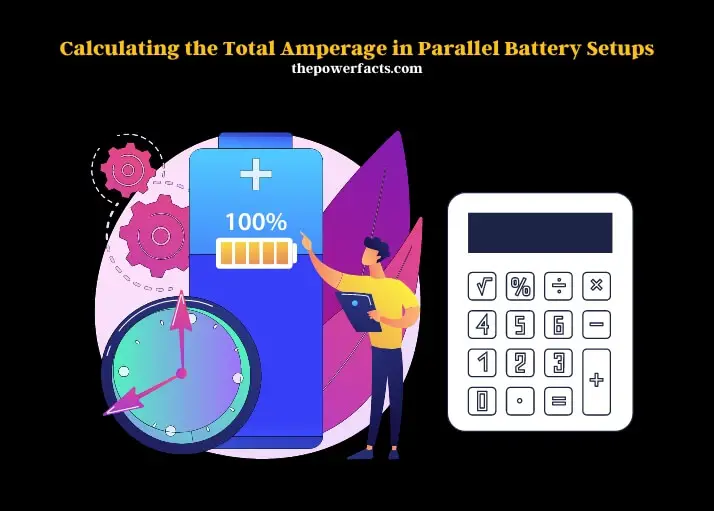
Best Practices for Installing Parallel 12V Batteries
Installing two 12V batteries in parallel involves more than just connecting them with the right wire gauge. Ensuring secure connections is paramount to prevent accidental disconnections or shorts. Proper insulation of the wires and terminals guards against environmental factors and reduces the risk of electrical hazards.
Regular maintenance and inspection of the battery system help in identifying and addressing potential issues before they lead to failures. Following these best practices ensures the longevity and reliability of the parallel battery setup.
Recommended Wire Gauge Sizes Based on Amperage and Length
Amperage Range | Length Range (feet) | Recommended Wire Gauge |
0-10A | 0-6 | 16 AWG |
10-20A | 0-6 | 14 AWG |
20-30A | 0-6 | 12 AWG |
30-40A | 0-6 | 10 AWG |
40-50A | 0-6 | 8 AWG |
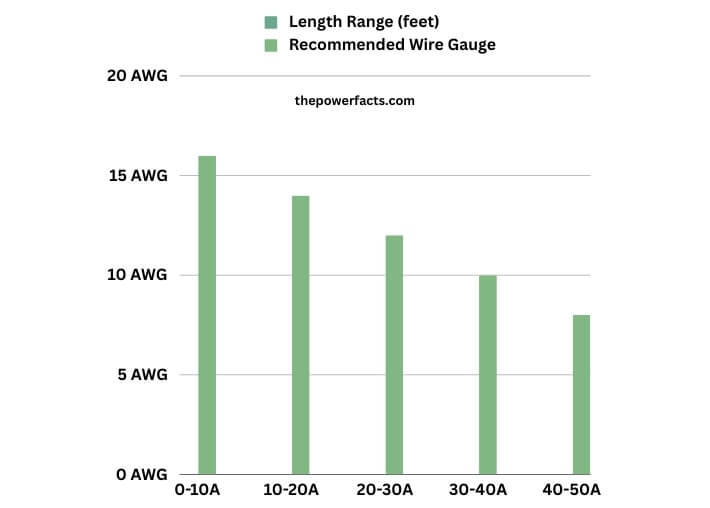
Comparison of Copper and Aluminum Wire Characteristics
Characteristic | Copper | Aluminum |
Conductivity Rating | High | Moderate |
Corrosion Resistance | Good | Less than copper |
Weight | Heavier | Lighter |
Cost Comparison | More expensive | Less expensive |
FAQs
How Does Temperature Affect Wire Gauge Choice?
Temperature plays a significant role in selecting the appropriate wire gauge for connecting two 12V batteries in parallel. As the ambient temperature increases, the conductivity of the wire can decrease, leading to higher resistance and potential overheating. It’s crucial to choose a wire gauge that can safely handle the expected current load without exceeding its temperature rating.
Wires with a higher temperature rating can carry more current without overheating, making them suitable for environments with elevated temperatures. This consideration ensures the longevity and safety of the battery system, preventing damage from excessive heat.
Can Wire Insulation Type Influence Gauge Selection?
The type of insulation on a wire affects its ability to withstand environmental conditions such as heat, cold, and moisture. Different insulation materials have varying levels of thermal resistance and physical durability. When connecting two 12V batteries in parallel, selecting a wire with insulation that can handle the operating environment is essential.
For example, wires with high-temperature insulation are preferable in hot climates, while those with moisture-resistant properties are ideal for damp conditions. The right insulation ensures the wire remains protected, maintaining its performance and safety over time.
What Role Does Wire Flexibility Play?
Flexibility is an important factor in wire selection for connecting two 12V batteries in parallel, especially in applications where the wire may need to be routed through tight spaces or around obstacles. Flexible wires are easier to install and reduce the risk of stress or damage at connection points.
It’s important to balance flexibility with the wire’s current-carrying capacity and resistance to ensure it can safely handle the power requirements of the battery system. Choosing a wire that combines the right level of flexibility with electrical performance ensures a reliable and durable connection.
How Important Is Wire Length Beyond Recommended Ranges?
While the recommended wire lengths aim to minimize voltage drop and resistance, there may be situations where longer wires are necessary. In such cases, it’s crucial to adjust the wire gauge accordingly to compensate for the increased resistance and potential voltage drop over longer distances.
Using a thicker wire gauge for extended lengths ensures that the current can be carried efficiently without significant losses, maintaining the performance and safety of the parallel battery system. This adjustment is vital for installations where the ideal wire length is not feasible.
Does the Number of Parallel Connections Affect Wire Gauge?
As the number of batteries connected in parallel increases, so does the total current flowing through the connecting wires. This requires careful consideration of the wire gauge to ensure it can handle the increased current without overheating. A higher capacity wire may be necessary to safely distribute the load among multiple batteries.
This consideration is crucial for systems with several batteries in parallel, as underestimating the wire gauge could lead to performance issues or safety hazards. Proper calculation of the total current helps in selecting the right wire gauge for the system’s needs.
Are There Special Considerations for Marine or Automotive Applications?
Marine and automotive environments pose unique challenges for connecting two 12V batteries in parallel, including exposure to moisture, vibration, and temperature fluctuations. In these settings, it’s important to choose a wire gauge that not only meets the electrical requirements but also is durable enough to withstand the environmental conditions.
Wires designed for marine or automotive use often have additional protective features such as corrosion-resistant coatings and vibration-resistant insulation. Selecting the appropriate wire gauge and type for these applications ensures the reliability and safety of the battery system in demanding conditions.
In conclusion, selecting the correct wire gauge for connecting two 12V batteries in parallel is a multifaceted decision that impacts the safety, efficiency, and reliability of the system. Considering factors such as electrical resistance, wire length, material properties, total amperage, and installation practices is essential for achieving an optimal setup. By adhering to the outlined best practices and making informed choices based on the specific requirements of the battery system, users can ensure a safe and efficient connection that meets their needs.