There are two main types of industrial control systems: direct digital control (DDC) systems and programmable logic controller (PLC) systems. Both types of systems have their own advantages and disadvantages, so the choice of which to use depends on the specific application. DDC systems are typically used for applications where real-time monitoring and response are required, such as in HVAC or process control.
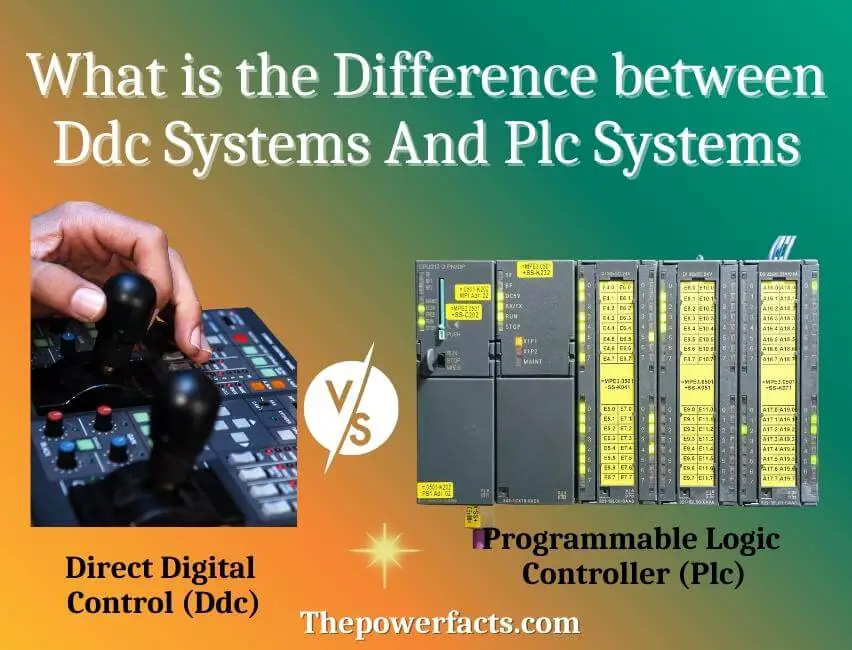
DDC systems consist of a central controller that receives input from sensors and then sends output to actuators to control the process. One advantage of DDC systems is that they can be very scalable – it is possible to add more controllers as needed to increase the size or complexity of the system. Another advantage is that DDC controllers often have built-in diagnostic capabilities, which can help identify problems with the system.
PLCs, on the other hand, are better suited for applications where there is a need for more flexibility in terms of programming. PLCs are programmable devices that can be programmed to perform a variety of tasks, such as controlling motors or monitoring inputs from sensors. PLCs are often used in manufacturing applications where there may be a need to change the production process on a regular basis.
One advantage of PLCs over DDC systems is that they can be easily reprogrammed to accommodate changes in the production process.
There are many different types of industrial automation systems available on the market today. Two of the most popular choices are DDC systems and PLC systems. But what is the difference between these two types of systems?
DDC systems, or Direct Digital Control systems, are typically used in larger industrial applications. They offer a higher degree of flexibility and functionality than PLCs, but they can also be more complex to set up and maintain. DDCs use a central controller to manage all of the devices in the system, and they communicate with these devices using digital signals.
This allows for more precise control over each device, and it makes it easier to make changes to the system if needed. PLCs, or Programmable Logic Controllers, are more commonly used in smaller industrial applications. They are simpler to set up and maintain than DDCs, but they don’t offer as much flexibility or functionality.
PLCs use a series of discrete input and output modules to control the devices in the system. These modules are connected together using analog or digital signals, depending on the specific PLC model.
What are the Main Components of a DDC System?
The direct-digital control (DDC) system is the brain of a building’s HVAC system. It constantly monitors and adjusts the heating, ventilation, and air conditioning (HVAC) equipment to maintain optimal conditions. A DDC system can be as simple as a single microprocessor that controls a single piece of equipment or as complex as a computer network that regulates an entire facility’s HVAC system.
The main components of a DDC system are:
Sensors | These devices measure various conditions in the controlled space such as temperature, humidity, CO2 levels, and pressure. The data from these sensors is used by the controller to make adjustments to the HVAC equipment. |
Controller | The controller is the “brain” of the DDC system. It uses data from the sensors to make decisions about how to adjust the HVAC equipment. controllers can be stand-alone units or they can be part of a larger computer network. |
Actuators | These devices carry out the commands from the controller and adjust the operation of the HVAC equipment accordingly. |
PLC Vs BMS
There are a few key differences between plc and BMS. For one, plc is more geared toward manufacturing and industrial applications while BMS is more focused on building automation. Plc also has more I/O capabilities than BMS, making it better suited for larger and more complex applications.
Finally, plc programming is typically done in ladder logic while BMS programming is done in a graphical interface.
DDC Vs BMS
The debate between DDC and BMS has been a hot topic in the HVAC industry for years. Both technologies have their proponents and detractors, but what’s the real difference? And which one is right for your application?
Let’s take a closer look. DDC (Direct Digital Control) technology has been around for decades and is the traditional choice for large-scale commercial applications. DDC systems are typically more expensive than BMS systems but offer greater flexibility and control.
With a DDC system, each individual piece of equipment (e.g., air handler, chiller, boiler) is controlled by its own dedicated controller. This allows for much finer control over each individual piece of equipment, as well as the ability to “tune” the system to specific conditions. BMS (Building Management System) technology is newer than DDC but has quickly gained popularity due to its lower cost and simpler installation.
A BMS system uses a single central controller to manage all of the equipment in a building or facility. While this can be less expensive than installing multiple controllers for each piece of equipment, it can also result in reduced flexibility and control. So which technology is right for you?
It depends on your specific needs and requirements. If you need maximum control over your equipment and conditions, then DDC is probably the way to go. However, if you’re looking for a simpler solution that won’t break the bank, then BMS may be the better choice.
DDC Vs DCS
There are two types of control systems used in the process industries – discrete and continuous. Discrete control systems (DCS) are those that use a finite number of states to represent the process variables, while continuous control systems (CCS) use a continuously variable representation. The main difference between DCS and CCS is in how they handle process variability.
In a DCS, the process variables are represented by a finite number of discrete states. This means that there is no direct relationship between the input and output variables – the mapping between them is done indirectly, through a set of rules or logic. This can make it difficult to tune a DCS to achieve the desired results.
In contrast, CCSs use a continuous variable representation of the process variables. This means that there is a direct relationship between the input and output variables, making it easier to tune the system to achieve the desired results. Another difference between DCS and CCS is in how they are implemented.
A DCS is typically implemented as hardware, with specialized software running on top of it. A CCS, on the other hand, can be implemented entirely in software, making it more flexible and easier to change or update.
DCS Vs PLC
When it comes to industrial automation, two of the most popular choices for control systems are DCS (distributed control system) and PLC (programmable logic controller). Both have their own advantages and disadvantages, so choosing the right one for your application can be a tough decision. Here’s a quick overview of each system to help you make a more informed choice.
DCS systems are typically used in larger industrial applications where there is a need for centralized control over a large number of process variables. DCS systems are also well-suited for processes that require tight regulation and close monitoring. One downside of DCS systems is that they can be complex to configure and maintain.
PLCs, on the other hand, are better suited for simpler applications with fewer process variables. PLCs are typically less expensive than DCS systems and easier to configure and maintain. However, PLCs may not provide the same level of precision or regulatory control as DCS systems.
DDC System HVAC
DDC system HVAC is an energy management system that helps to reduce the cost of heating and to cool a building. It does this by automatically controlling the temperature, ventilation, and air conditioning in a building. The DDC system can be programmed to suit the specific needs of the occupants of a building, making it more energy efficient.
Siemens DDC Controller
A digital control panel is a device that helps to manage and automate the operations of a facility or process. It is also known as a distributed control system (DCS) or programmable logic controller (PLC). A digital control panel typically consists of input/output modules, controllers, power supplies, and communication ports.
Siemens DDC Controller is one type of digital control panel. It uses Fieldbus technology to connect various devices in an industrial environment. Fieldbus technology allows for data exchange between devices without the need for dedicated wiring.
This makes installation and maintenance simpler and more cost-effective.
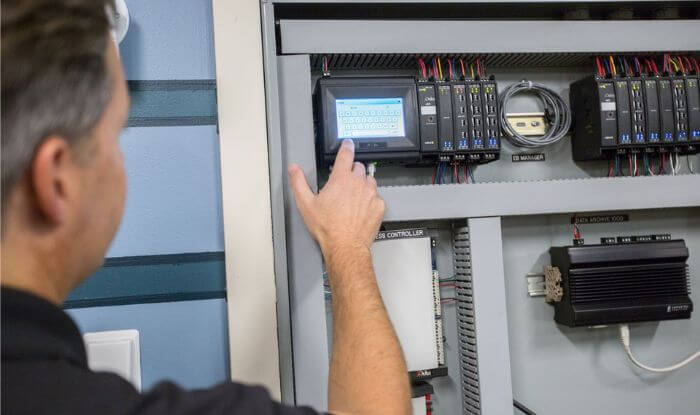
Can PLCS Be Used for DDC?
PLCs can be used for DDC, but there are some key differences that need to be considered. For example, PLCs typically have a more limited number of inputs and outputs than DDC systems. This can make it more difficult to connect all the necessary sensors and actuators to the PLC.
In addition, PLCs often do not have as much processing power as DDC systems, so they may not be able to handle the same amount of data or perform complex calculations as quickly. Finally, PLCs are typically designed for use in industrial applications, while DDC systems are more often used in commercial buildings.
What is the Difference Between DDC And DCS?
DDC and DCS are both industrial control systems that are used to manage and automate processes. They both have their own strengths and weaknesses, but the main difference between them is that DDC is a more centralized system while DCS is more distributed. DDC systems tend to be more expensive and complex, but they offer more flexibility and scalability.
DCS systems are less expensive and easier to implement but are not as flexible or scalable.
Which is Better DCS Or PLC?
There is no one-size-fits-all answer to this question, as the best system for a given application depends on a number of factors. However, in general, DCS systems tend to be more complex and expensive than PLCs, while PLCs are more suited for simpler applications.
What is the Difference Between PLC And BMS?
PLC is an acronym for the programmable logic controller. A PLC is a computer used to control industrial machines and processes. BMS stands for building management system.
A BMS is a computerized system that controls and monitors the mechanical and electrical equipment in a building.
Wrap Up
The difference between DDC systems and PLC systems is that DDC systems are typically used for smaller applications while PLC systems are used for larger, more complex applications. Both types of systems have their own advantages and disadvantages, so it is important to choose the right type of system for the application.