The appropriate gauge wire for parallel batteries depends on the system’s total current and voltage requirements. It is essential to select a wire gauge that can safely handle the expected electrical load without overheating.
When configuring parallel battery systems, the choice of wire gauge is a critical factor that influences both the efficiency and safety of the setup. The primary consideration in selecting the wire gauge is the ampacity, or the maximum current that the wire can safely conduct. Using a wire that is too thin for the current load can lead to excessive heat generation, posing a risk of fire and reducing the efficiency of power transmission. On the other hand, excessively thick wires may be unnecessarily costly and cumbersome.
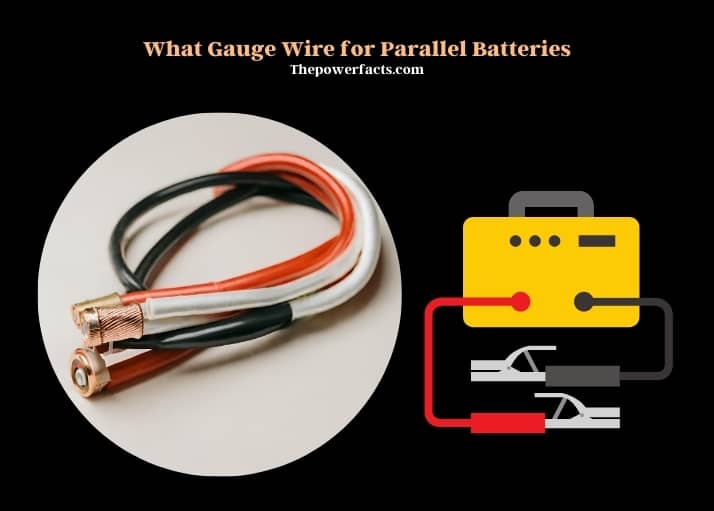
The length of the wire run also plays a significant role in this decision. Longer wire runs experience more significant voltage drops, necessitating the use of thicker wires to minimize power loss.
In addition to the electrical considerations, environmental factors such as temperature and exposure to the elements should be taken into account. Wires in hotter environments or those exposed to physical stress may require a higher gauge to ensure durability and consistent performance.
The goal is to balance safety, efficiency, and cost. Consulting with a professional or referring to standard wire gauge charts based on the specific requirements of the battery system can guide in making an informed decision. This careful selection ensures that the parallel battery system operates optimally, providing reliable power while maintaining safety standards.
Optimal Wire Gauge for Parallel Battery Systems
Selecting the appropriate wire gauge for parallel battery setups is a critical decision impacting system performance and safety. The electrical resistance in parallel circuits plays a pivotal role in this selection. Lower resistance in thicker wires reduces heat generation, thereby enhancing efficiency and safety. Ampacity, or the maximum current that a wire can handle, is another crucial factor. It’s essential to choose a wire gauge that can safely carry the expected load without overheating.
Safety considerations are paramount, especially in preventing short circuits and fires. Adhering to wire gauge standards, such as the American Wire Gauge (AWG) system, ensures compatibility and reliability. These standards provide a guide for selecting the right wire gauge based on current load and circuit length.
Wire Gauge: Its Impact on Battery Performance
The choice of wire gauge significantly affects battery efficiency and longevity. A primary concern is the voltage drop across the wire. Excessive voltage drop can lead to inefficient power delivery and increased energy loss. This inefficiency is more pronounced in systems with long wire runs or high current demands.
Heat generation is another critical factor. Wires that are too thin for the current load can overheat, leading to insulation damage and potential fire hazards. This heat also negatively impacts battery lifespan, as excessive temperature can degrade battery cells over time.
Ensuring optimal power delivery involves balancing the wire gauge with the system’s power requirements. This balance ensures that the batteries operate within their optimal efficiency range, prolonging their lifespan and maintaining consistent performance.
Comparative Wire Gauge Analysis in Various Applications
Wire gauge requirements vary significantly between residential and industrial parallel battery applications. Residential systems generally have lower power demands, allowing for thinner wires compared to industrial setups, which often require thicker wires due to higher power and longer run requirements.
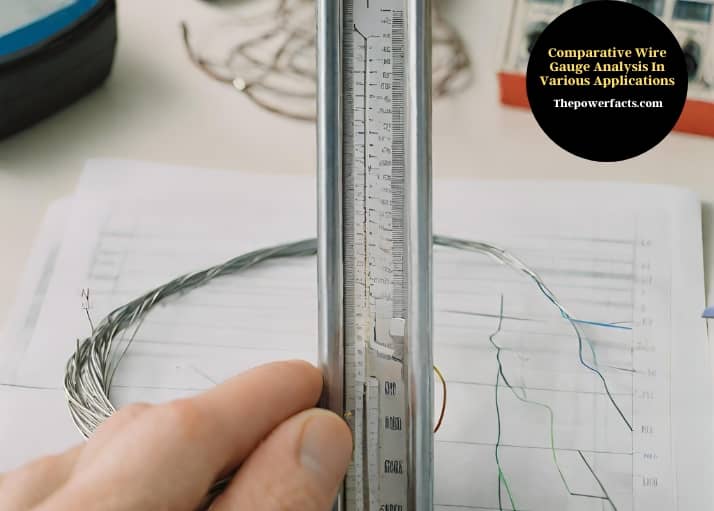
A data table comparing wire gauges in different applications provides a clear perspective on this variation. For instance, a residential solar battery system might use 12 AWG wires for short runs, while an industrial setup with longer runs and higher loads might require 6 AWG or thicker.
Application Type | Typical Wire Gauge | Load Capacity | Run Length |
Residential Solar Battery | 12 AWG | Up to 20A | <50 feet |
Industrial Energy Storage | 6 AWG | Up to 60A | >100 feet |
This table illustrates the need for different wire gauges based on application-specific requirements.
Wire Gauge Selection in Renewable Energy Systems
Renewable energy systems, such as solar and wind power, have unique requirements for wire gauge selection. These systems often involve long wire runs from the energy source to the storage or usage point, necessitating careful consideration of wire size to minimize losses.
Environmental factors also play a role. Outdoor installations must contend with temperature fluctuations and potential physical damage, requiring more robust wiring solutions.
A data table on wire gauge recommendations for renewable energy systems can guide installers and designers in making informed decisions.
System Type | Recommended Wire Gauge | Considerations |
Solar Panel to Battery | 10 AWG | Long runs, outdoor exposure |
Wind Turbine to Battery | 8 AWG | High current, variable loads |
These recommendations ensure efficient energy transfer and system longevity.
Advanced Wire Gauge Considerations for High-Demand Systems
High-demand systems, such as electric vehicle charging stations and large-scale energy storage, require meticulous wire gauge selection. These systems often deal with high currents and are critical to the reliability and safety of the infrastructure they support.
Peak load management is a significant consideration. The wire gauge must be capable of handling peak loads without overheating or losing efficiency. Future technology trends, such as the increasing prevalence of electric vehicles, also dictate the need for scalable and adaptable wiring solutions.
In these high-demand scenarios, the wire gauge is not just a component choice but a fundamental aspect of system design, impacting everything from safety to operational efficiency.
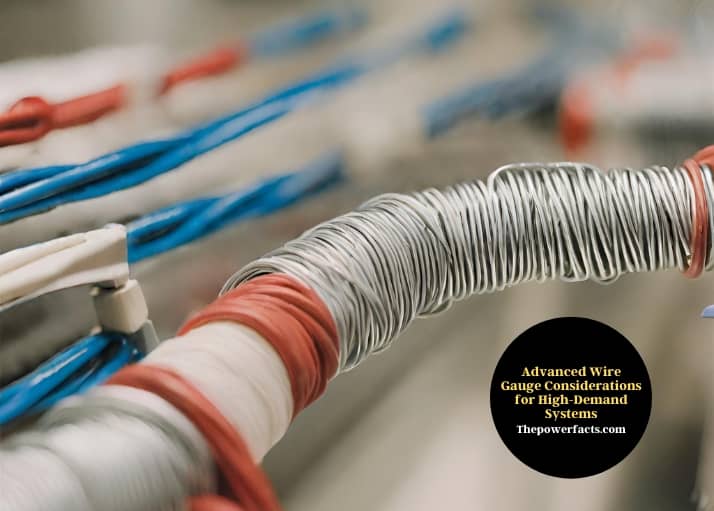
FAQs
How Does Wire Gauge Affect Battery Charging Speed?
The wire gauge in parallel battery setups significantly influences the charging speed. Thicker wires, with a lower gauge number, have less resistance, allowing for faster and more efficient charging. This is because lower resistance minimizes energy loss as heat, ensuring more power reaches the batteries. In contrast, thinner wires can slow down the charging process due to higher resistance, leading to more significant energy loss and reduced charging efficiency. Therefore, selecting an appropriate wire gauge is crucial for optimizing the charging speed of parallel battery systems.
Can Wire Gauge Impact Overall System Cost?
Yes, the wire gauge can substantially affect the overall cost of a parallel battery system. Thicker wires, which are lower in gauge, are generally more expensive due to the higher amount of material used.
They offer better efficiency and safety, potentially reducing long-term costs related to energy loss and maintenance. On the other hand, opting for thinner, higher gauge wires might lower initial expenses but can lead to increased energy loss and potential safety risks, which could incur additional costs over time. Balancing cost and performance is key when selecting wire gauge.
What Role Does Wire Gauge Play in System Safety?
Wire gauge plays a crucial role in the safety of parallel battery systems. Inadequately sized wires can overheat, especially under high current loads, posing a fire hazard. Thicker wires, with lower gauge numbers, are better equipped to handle higher currents without excessive heating, thereby reducing the risk of fire and other safety issues. It’s essential to choose a wire gauge that matches the system’s current requirements to ensure safe operation. Regular inspections and adherence to safety standards are also vital in maintaining system safety.
How to Determine the Ideal Wire Gauge for Specific Battery Types?
Determining the ideal wire gauge for specific battery types involves considering the battery’s voltage and current requirements. Batteries with higher voltage and current ratings typically require thicker, lower gauge wires to handle the increased power flow without significant energy loss or overheating. It’s important to consult the battery manufacturer’s specifications and possibly seek expert advice to ensure the chosen wire gauge is suitable for the specific battery type and the system’s overall power requirements.
Does Wire Gauge Influence System Efficiency in Extreme Temperatures?
Wire gauge can influence system efficiency in extreme temperatures. In cold environments, resistance in wires increases, potentially reducing efficiency. Thicker wires, with lower gauge numbers, can mitigate this effect due to their inherently lower resistance. Conversely, in hot environments, the risk of wire overheating is heightened, especially if the wire gauge is too high (thin). Using an appropriately thick wire ensures better performance and reduces energy loss in varying temperature conditions, maintaining system efficiency.
Is Wire Gauge Selection Different for Short vs. Long Battery Runs?
Wire gauge selection indeed varies between short and long battery runs. For short runs, thinner wires might suffice as the energy loss due to resistance is less significant over shorter distances.
For longer runs, thicker wires are preferable to minimize energy loss and voltage drop over the distance. The increased resistance in longer wire runs can significantly impact efficiency and performance, making the choice of a lower gauge (thicker) wire more critical to ensure effective power transmission in parallel battery systems.
Summary
The selection of the right wire gauge for parallel battery systems is a nuanced process that hinges on various factors, including application type, safety requirements, efficiency concerns, and future scalability. From residential to industrial applications, and especially in renewable energy systems and high-demand scenarios, the choice of wire gauge plays a crucial role in the overall performance and longevity of the system. By understanding these diverse needs and adhering to established standards, one can ensure optimal system functionality and safety.