The battery management system (BMS) is a critical component in any electric vehicle (EV). Its primary function is to ensure that the batteries are operating within their safe limits, while also providing information to the rest of the EV systems about the state of charge (SOC), voltage, and temperature of the batteries. There are four main components to most BMSs: sensors, a control unit, a communication interface, and a cooling system.
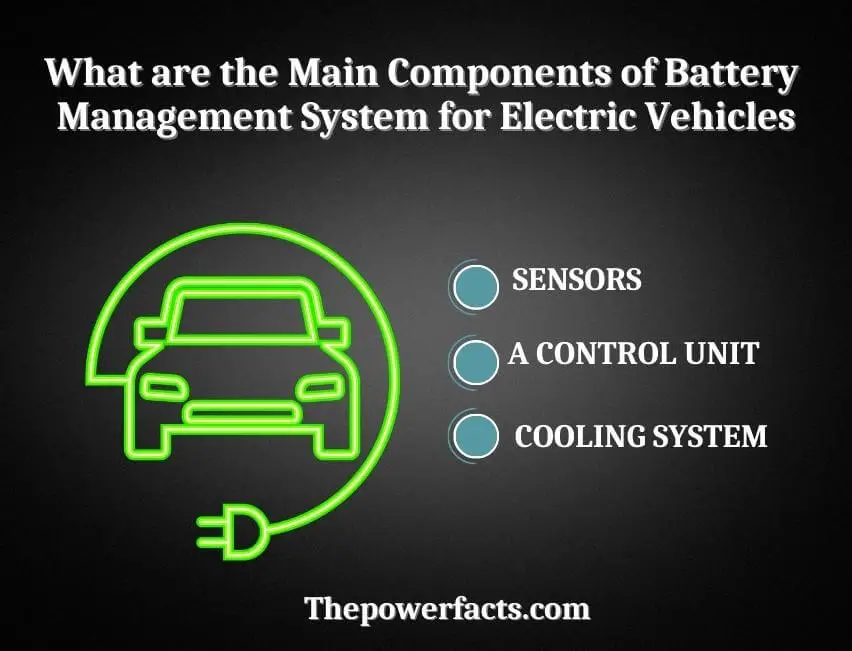
The sensors constantly monitor the SOC, voltage, and temperature of each individual battery cell. This information is then fed to the control unit which uses algorithms to determine if any adjustments need to be made to charging or discharge rates in order to maintain optimal battery health. The communication interface allows the BMS to send data about battery status to other EV systems and receive commands from them.
Finally, the cooling system helps keep the batteries at their ideal operating temperature by circulating coolant around them as needed.
Batteries are critical components in electric vehicles (EVs). A typical EV battery pack consists of multiple cylindrical or prismatic cells connected in series and/or parallel. The capacity of an EV battery pack ranges from several kilowatt-hours to over 100 kWh.
The voltage of an EV battery pack can range from hundreds to thousands of volts. A Battery Management System (BMS) is a system that monitors, manages, and protects batteries in EVs. BMSes typically have three main functions: cell balancing, monitoring, and protection.
Cell balancing ensures that all cells in an EV battery pack are equally charged and discharged. Monitoring provides data about the status of the battery pack, such as voltage, current, temperature, and state of charge. Protection prevents the battery pack from being damaged by overcharging, over-discharging, overheating, or short-circuiting.
There are many different types of BMSes on the market today. Some BMSes are designed for specific types of batteries, while others can be used with any type of battery. When choosing a BMS for your EV project, it is important to select one that is compatible with the type of batteries you are using and that has the features you need.
What are the Components of a Battery Management System for Electric Vehicles?
The electric vehicle battery management system (BMS) is a critical subsystem that regulates the state of charge (SoC) and state of health (SOH) of the lithium-ion batteries in an EV. The BMS also provides thermal management to keep the batteries within their operating temperature range. The main components of an EV battery management system are:
1. Battery cells | These are the basic units that store energy in a chemical form and release it as electrical energy. |
2. A cell balancing circuit | This equalizes the voltage across all cells in the battery pack to prevent overcharging or undercharging of any individual cell. |
3. A control unit | This manages all activities related to charging and discharging the battery, including monitoring SoC, SOH, and temperature levels; controlling the flow of current; and protecting the cells from damage due to overloading or overheating. |
4. A power converter | This converts DC power from the batteries into AC power for use by the drive motor. |
What are the Three Main Components of a Battery Electric Vehicle?
A battery electric vehicle (BEV) is a type of electric vehicle that uses a battery to store energy and power the vehicle’s motors. The three main components of a BEV are:
1. The Battery: This is the heart of the BEV and stores all the electrical energy that powers the vehicle.
2. The Electric Motor: This converts the stored electrical energy from the battery into mechanical energy, which turns the wheels and propels the vehicle forwards. 3. The Controller: This regulates how much power is sent from the battery to the motor, based on input from things like the accelerator pedal or brake pedal.
What is Electric Vehicle Management System?
An electric vehicle management system (EVMS) is a system that helps to optimize the operation and performance of an electric vehicle (EV). It can be used to monitor battery status, track driving habits, and even control charging times. EVMS systems can be either stand-alone units or integrated into other car systems such as navigation units.
The main purpose of an EVMS is to help improve the range and efficiency of an electric vehicle. For example, by monitoring the state of charge of the batteries, an EVMS can help drivers avoid “range anxiety” by knowing when it is time to recharge. Additionally, by tracking driving habits, an EVMS can provide feedback to drivers on how they can drive more efficiently and conserve power.
In some cases, an EVMS can even control charging times so that batteries are not overcharged or damaged. While there are many different types of EVMS on the market, most share a few common features. These features may include a display that shows battery status and estimated range; inputs for data such as odometer readings and charge levels; outputs for controlling things like charging times; and software for analyzing data and providing feedback to drivers.
What is Inside Battery Management System?
A Battery Management System (BMS) is a system that monitors and regulates batteries. It ensures that the battery is charged correctly and does not overheat. The BMS also protects the battery from being overloaded or damaged.
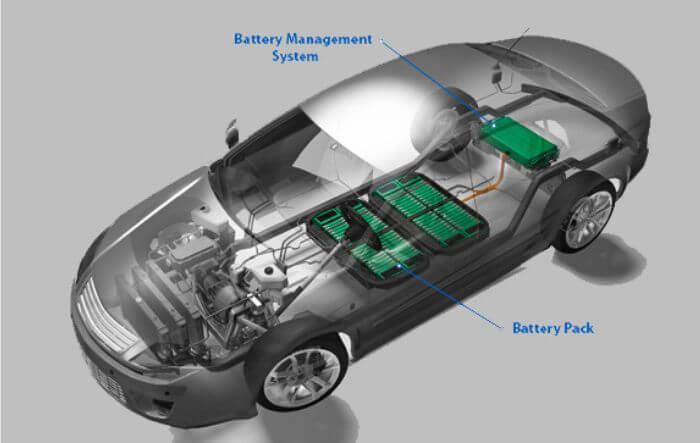
Battery Management System for Electric Vehicle
As the cost of electric vehicles (EVs) continues to fall and their range and performance continue to improve, more and more consumers are making the switch from gas-powered cars to EVs. But one of the challenges that still needs to be addressed is how to manage batteries so they last as long as possible and don’t degrade too quickly. That’s where battery management systems (BMS) come in.
A BMS is a computerized system that monitors and manages an EV’s battery pack, ensuring that it stays within safe operating limits and doesn’t overcharge or overdischarge. There are many different types of BMS on the market, but they all perform the same basic functions. Here’s a look at how BMS work and what they can do for your EV.
How Battery Management Systems Work? A typical battery pack for an EV consists of multiple cells connected in series or parallel. Each cell has its own voltage level that needs to be monitored, so a BMS will usually have multiple channels, each dedicated to monitoring one cell voltage.
What is Battery Management System for Electric Vehicle?
An electric vehicle’s battery management system (BMS) is a critical component that ensures the safety and performance of the battery pack. The BMS monitors the individual cell voltages and temperatures, and balances the cells to ensure they are all operating within their safe operating limits. The BMS also protects the cells from over-charging, over-discharging, and excessive current draw.
The BMS is an essential part of any electric vehicle, as it manages the high voltage battery pack and ensures its safety and performance.
Battery Management System Design for Electric Vehicle
As the number of electric vehicles (EVs) on the road continues to increase, so does the demand for effective battery management systems (BMS). A BMS is responsible for monitoring and managing a vehicle’s battery pack to ensure optimal performance and longevity. There are many factors that need to be considered when designing a BMS for an EV, including:
1. The type of battery being used (lithium ion, lead acid, etc.)
2. The size of the battery pack
3. The voltage and current requirements of the system
4. The operating environment (temperature, humidity, etc.).
The first step in designing an effective BMS is to understand the specific needs of the application. Once these needs have been identified, it is important to select components that are compatible with both the batteries and the system as a whole.
For example, choosing a BMS controller that can handle high currents is critical if the EV will be used for frequent starts and stops. Similarly, selecting sensors that are accurate at low temperatures is important if the vehicle will be operated in cold climates.
Battery Management System for Lithium-Ion Battery
Most people are familiar with the term “battery management system” (BMS), but may not know exactly what it refers to. A BMS is an electronic system that monitors and manages a rechargeable battery pack. The key functions of a BMS are to protect the battery pack from operating outside its safe operating limits, balancing the cells in the pack so that they all deliver the same discharge capacity, and providing data on the status of the battery pack to allow its use to be monitored.
The main components of a BMS are a microcontroller, sensors, and control circuitry. The microcontroller is the “brain” of the system and carries out all of the decision making based on input from the sensors. The sensors measure various parameters such as cell voltage, temperature, current flow, etc.
Based on these readings, the microcontroller will take appropriate action such as shutting down the power if any unsafe conditions are detected or balancing cells that have different voltages. The control circuitry provides power to various parts of the system and also handles communication with external devices such as a charger or display unit. A lithium-ion battery pack will typically have one BMS board for each cell in the pack.
For example, a 10S4P pack (10 cells in series, 4 parallel strings) would require 10 BMS boards. Each board will monitor 4 cells so in this case 40 cells would be monitored by 10 boards resulting in each board monitoring 4 adjacent cells. This type of configuration is known as “series balance” because each board only needs to sense voltage differences between adjacent cells (cells in series).
Another common configuration is “parallel balance” where each board monitors allcells in one parallel string (4 boards would be required for our 10S4P example). Regardless of which configuration is used, it’s important that all batteries in a given pack be balanced together so that no single cell experiences excessive stress due to overcharging or deep discharge cycles. Lithium-ion batteries are very sensitive to overcharging and can be easily damaged if allowed to charge above their maximum voltage limit.
For this reason, it’s vitally important that any lithium-ion battery pack has some form of overcharge protection built into its BMS design. When an overcharge condition is detected by the BMS sensor inputs, immediate action must be taken to shut off power before serious damage occurs.
Battery Management System Architecture
A battery management system (BMS) is a critical subsystem in any application that uses batteries. Its purpose is to ensure the safe and reliable operation of a battery pack by protecting it from damage and maximizing its performance and lifetime. The BMS consists of three main components: a control unit, one or more sensing units, and a power unit.
The control unit is the brains of the system, responsible for monitoring the status of the battery pack and making decisions about when to charge or discharge it. The sensing units provide information about the current state of the battery pack to the control unit. This can include things like temperature, voltage, current, and capacity.
The power unit provides power to charge or discharge the battery pack as directed by the control unit. There are many different architectures for BMSs, but they all share these basic components. The specific implementation will be determined by factors such as the type of batteries used, desired features, cost constraints, etc.
One common architecture is known as an active balancing BMS. This type of system constantly monitors each cell in the battery pack and balances them so that they are all at equal levels of charge. This helps to prevent overcharging or deep discharging of any one cell, which can damage it or shorten its lifespan.
Active balancing BMSs typically use multiple sense wires per cell so that they can accurately monitor each cell’s voltage level without introducing too much resistance into the circuit. Another popular architecture is called a passive balancing BMS. This type of system does not actively monitor or balance individual cells in the battery pack.
Instead, it relies on each cell’s self-discharge rate to keep itself balanced over time.
Disadvantages of Battery Management System
A battery management system (BMS) is a device or set of devices that monitors, regulates and protects batteries from overcharging, deep discharge and other conditions that can shorten their lifespan. A BMS can be stand-alone, or it can be integrated into the design of the battery pack. While a BMS offers many advantages, there are also some potential disadvantages to consider.
Point One
One disadvantage of a BMS is that it adds complexity to the battery pack. This can make the pack more expensive to manufacture and more difficult to troubleshoot if problems arise. Additionally, a BMS can add weight and bulk to the battery pack, which may be undesirable in some applications.
Point Two
Another potential downside of using a BMS is that it can introduce new failure points into the system. If the BMS itself fails, it could cause the entire battery pack to fail. Additionally, if communication between the BMS and individual cells in the pack breaks down, this could also lead to problems.
Point 3
Overall, a battery management system can offer many benefits for safeguarding batteries against damage and prolonging their lifespan. However, there are also some potential drawbacks to consider before deciding whether or not to use one in your application.
Introduction to Battery Management System
A battery management system (BMS) is a device that controls, monitors, and protects batteries in electronic devices. It ensures the safe operation of batteries by preventing overcharging, deep discharge, and excessive heat. A BMS also prolongs the life of batteries by balancing the cells and equalizing the voltage.
Most BMS systems are made up of three parts: a control unit, sensors, and actuators. The control unit is the brains of the system and contains a microcontroller or microprocessor that receives data from the sensors and sends commands to the actuators. The sensors monitor factors such as temperature, voltage, current, and capacity.
The actuators carry out commands from the control unit such as disconnecting or reconnecting battery cells. BMS systems can be used in a variety of applications including electric vehicles (EVs), solar energy systems, UPS systems, consumer electronics devices, and more. Many EVs on the market today come equipped with a BMS to ensure safety and optimal performance of the battery pack.
Solar energy systems also use BMS units to protect against overcharging during peak sunlight hours. UPS systems utilize BMS units to prevent damage to sensitive equipment caused by power surges or blackouts. Consumer electronics devices such as laptops or cell phones often have built-in BMS units to protect against overcharging when connected to an external power source for too long.
Battery Management Software
As electronic devices become more sophisticated, the demand for better battery management software (BMS) increases. A BMS is a system that helps optimize the use of a rechargeable battery by monitoring its state and temperature and adjusting charging and discharge accordingly.
Most BMS systems on the market today are designed for lithium-ion batteries, which are used in laptops, cell phones, digital cameras, and electric vehicles, among other things.
Lithium-ion batteries are notoriously finicky, so a good BMS can prolong their life and prevent them from catching fire or exploding.
There are two main types of BMS: centralized and distributed. Centralized systems have one central controller that monitors all of the cells in a battery pack.
Distributed systems have each cell monitored by its own individual circuit board. Both types have their pros and cons, but distributed systems are generally more expensive and complex to design.
Batteries are made up of cells that store energy in chemical form.
When a device is plugged into an outlet to charge, electrons flow from the power source into the positive electrode of the cell (the anode). This process is called oxidation because it causes the anode to oxidize (lose electrons). During discharge, when a device draws power from the battery, electrons flow from the negative electrode of the cell (the cathode) through an external circuit back to the positive electrode.
This process is called reduction because it causes the cathode to reduce (gain electrons). The overall effect is that energy flows from one end of the cell to the other during charging and discharge cycles.
A typical lithium-ion cell has four electrodes: two metal current collectors (one at each end), a porous separator between them, and active materials coated onto each current collector.
The active material on the anode side is usually lithium metal oxide (LiCoO2), while that on the cathode side is typically lithium cobalt oxide (LiCoO2). As these names suggest, there are many different chemistries used for both anodes and cathodes in commercial cells; however, most commercially available cells use one of these two basic chemistries.
Final Thoughts
Today, we will be discussing the main components of a battery management system for electric vehicles. A battery management system is responsible for ensuring that the batteries in an electric vehicle are operating correctly and efficiently. The system monitors the voltage, current, and temperature of the batteries and provides information to the vehicle’s control unit.
The system also manages the charging and discharging of the batteries to maximize their lifespan. The four main components of a battery management system are:
Battery pack | This is the group of batteries that power the electric vehicle. The pack contains multiple individual cells that are connected together. |
Battery monitor | This component constantly monitors the voltage, current, and temperature of each cell in the battery pack. It sends this information to the BMS controller so that it can make decisions about how to best manage the battery pack. |
BMS controller | This is the brains of the operation. The controller uses information from the battery monitor to make decisions about when to charge or discharge the batteries. It also controls other aspects of battery management, such as balancing between different cells in order ensure they all age evenly. |
Display | This component provides information about the status of the battery pack tothe driver or owner ofthe electric vehicle. It can be as simple as a few LEDs or a more complex LCD display with detailed data aboutthe current stateofcharge, estimated range remaining, etc. |