There is no doubt that PLCs can be used for DDC, but the question is how effective they are. While PLCs offer some advantages over traditional controllers, they also have some significant disadvantages. In the end, it depends on the specific application and what trade-offs are acceptable.
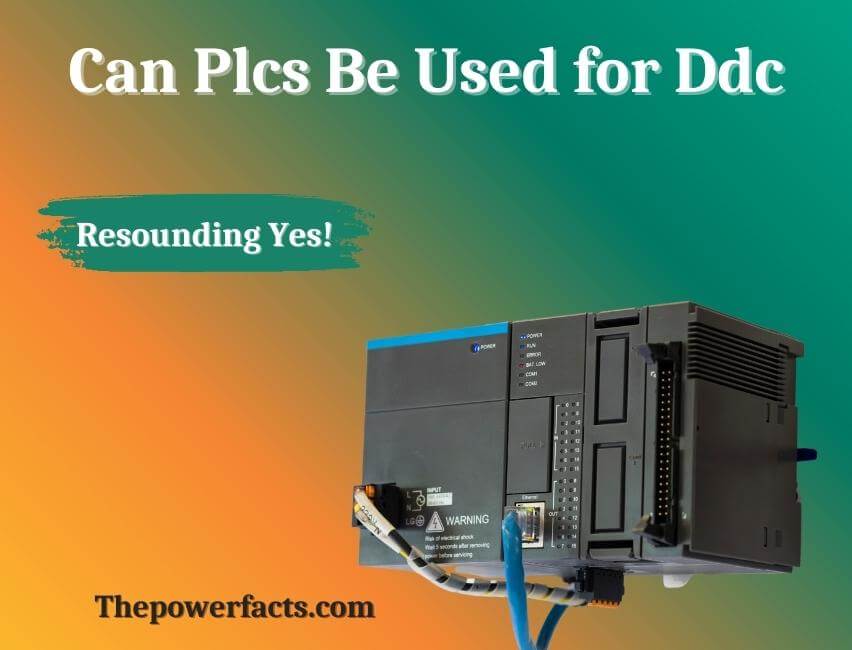
As more and more devices are added to the Internet of Things, the question arises as to whether traditional PLCs can be used for DDC (direct digital control). The answer is a resounding yes! PLCs were designed for industrial applications, which often require precise control over various processes.
This same level of precision can be applied to managing the myriad devices that make up the IoT. In fact, many manufacturers are already offering PLC-based solutions for DDC applications.
PLC Vs BMS
There are two main types of building automation systems – Plc and Bms. Both have their own advantages and disadvantages, so it’s important to choose the right one for your needs. Plc stands for the programmable logic controller.
It’s a type of device that uses software to control industrial machinery and processes. PLCs are widely used in many industries, including manufacturing, oil and gas, food and beverage, pharmaceuticals, and more.
Advantages of PLCs Include
– They’re simple to use and easy to program.
– They’re rugged and reliable.
– They offer a high degree of flexibility.
Disadvantages of PLCS Include
– They can be expensive.
– They require skilled personnel to operate and maintain them.
– They can be complex to program if you don’t have experience with programming languages like ladder logic or C++.
DDC Vs DCS
DDC Vs DCS There are two types of DCS: distributed control system (DCS) and programmable logic controller (PLC). Both systems have their own advantages and disadvantages.
Here is a comparison of the two types of DCS.
Advantages of DCS
1. Better Process Control
Because each device in the system has its own dedicated processor, devices can be controlled more independently and precisely.
This leads to better overall process control.
2. Greater Flexibility
DCSs are easier to reconfigure than PLCs. This makes them well-suited for applications where processes frequently change or where new processes need to be added often.
3. More Scalability
It is easier to add new devices to a DCS than a PLC, making DCSs more scalable than PLCs.
4. Higher Availability
Since each device in a DCS has its own dedicated processor, if one device fails, the rest of the system can continue operating normally; this is not the case with PLCs, where a single point of failure can bring down the entire system.
Disadvantages of DCS
1. Higher Initial Cost
Because each device in a DCS has its own dedicated processor, DC systems tend to be more expensive than PLC systems upfront.
2. More Complex Commissioning and Maintenance
Since each device in a DCS must be configured individually, commissioning and maintenance tend to be more complex and time-consuming than with PLCs.
DDC Vs BMS
There are many different types of battery management systems (BMS) on the market today. Two of the most popular brands are DDC and BMS. So, what is the difference between these two brands?
DDC offers a more comprehensive system that includes features like voltage balancing, cell temperature monitoring, and over-voltage protection. DDC also has a built-in display that shows you all the important information about your battery pack in one place. BMS, on the other hand, focuses on providing accurate voltage readings and doesn’t include some of the bells and whistles that DDC offers.
So, which brand is right for you? It really depends on your needs. If you need a complete system with all the bells and whistles, then DDC is probably your best bet.
But if you just need something to give you accurate voltage readings, then BMS will suffice.
PLC Panel Full Form
PLC stands for the programmable logic controller. It is a type of electronic device that is used to control machines and processes. PLCs are widely used in industrial and commercial applications.
A PLC panel is a physical interface between the user and the PLC. It consists of a number of switches, lights, and other devices that allow the user to interact with the PLC.
What are the Main Components of a DDC System?
A DDC system, or direct digital control system, is a type of building automation system that controls temperature, ventilation, and air conditioning systems. It is a computer-based control system that uses sensors to monitor various conditions in a space and then adjusts the HVAC settings to maintain comfortable conditions. DDC systems are typically more accurate and responsive than traditional mechanical thermostats and can provide significant energy savings by reducing heating and cooling costs.
In addition, DDC systems can be integrated with other building automation systems to provide even greater efficiency and control. The main components of a DDC system include:
Sensors | Sensors are used to monitor various conditions in a space, such as temperature, humidity, carbon dioxide levels, etc. These sensors send signals to the controller which then adjusts the HVAC settings accordingly. |
Controller | The controller is the brain of the operation; it receives input from the sensors and then makes decisions about how to adjust the HVAC settings. Controller types include microprocessor-based controllers, PLCs (programmable logic controllers), and dedicated hardware controllers. |
actuators | Actuators are used to physically adjust the HVAC settings in response to commands from the controller. Common actuators include damper motors (for adjusting air flow), valve motors (for adjusting water flow), and VFDs (variable frequency drives for controlling fan speed). |
BMS DDC Panel Full Form
BMS DDC Panel Full Form What is a BMS DDC panel? A BMS (Building Management System) DDC (Direct Digital Control) panel is a type of control panel used to manage the heating, ventilation, and air conditioning (HVAC) systems in a building.
The BMS DDC panel allows for remote monitoring and control of the HVAC system, as well as other building systems such as security and lighting. The BMS DDC panel typically consists of a touchscreen interface that allows the user to access various functions and features. The interface can be used to set temperature settings, view energy usage data, and even monitor the status of individual HVAC components.
In some cases, the BMS DDC panel may also include a keypad or other input device for manual operation. Why use a BMS DDC panel? There are many benefits to using a BMS DDC panel in your building.
Perhaps the most important benefit is increased efficiency. By remotely monitoring and controlling the HVAC system, you can make sure that it is operating at peak efficiency at all times. This can lead to significant savings on your energy bills over time.
In addition to increased efficiency, using a BMS DDC panel can also help improve indoor air quality by allowing you to monitor and adjust air flow within the building. Additionally, it can help reduce wear and tear on HVAC components by automatically making adjustments based on real-time conditions.
DDC Controller Honeywell
A DDC controller is a type of device that is used in order to control the heat, ventilation, and air conditioning (HVAC) systems in a building. This type of device is usually connected to a computer network in order to allow for remote monitoring and control of the HVAC system. The Honeywell DDC controller is a popular choice for many buildings, as it offers features such as real-time energy consumption monitoring, demand-based heating and cooling, and the ability to integrate with other building systems.
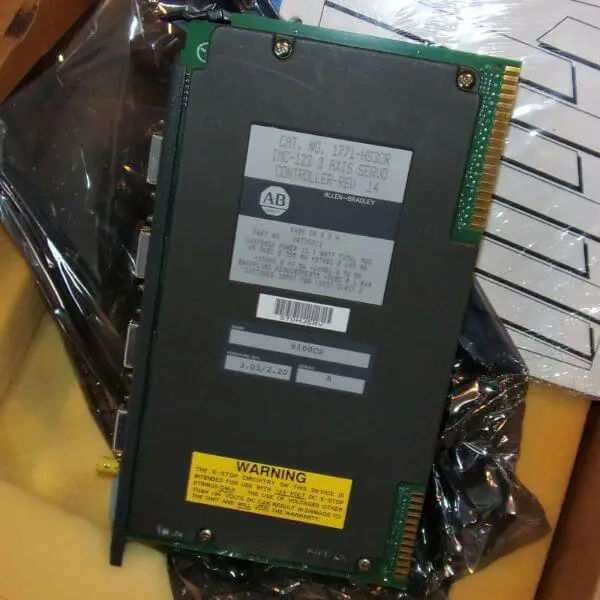
What’s the Difference Between PLC And DDC?
The difference between PLC and DDC is that PLC uses a ladder logic programming language while DDC uses a more traditional programming language. PLC is typically used in industrial applications while DDC is used in more commercial applications.
Can a PLC Be Part of a DCS?
Yes, a PLC can be part of a DCS. A PLC is a programmable logic controller, which is a type of computer that is used to control industrial machines and processes. A DCS is a distributed control system, which is a type of system that uses multiple controllers to manage complex processes.
Are PLC And DCS the Same?
PLC and DCS are two different types of systems that are used to control industrial processes. PLCs (Programmable Logic Controllers) are typically used in manufacturing or production environments where there is a need for precise control over processes. DCS (Distributed Control Systems) on the other hand, are more commonly used in process-oriented industries such as oil and gas, chemical processing, etc.
The main difference between PLC and DCS is that PLCs focus on logic and sequencing while DCS systems focus on continuous monitoring and manipulation of data. In terms of architecture, PLCs tend to be centralized with all controllers being located in one place. On the other hand, DCS systems are distributed with controllers located throughout the facility.
This allows for better flexibility and scalability. In terms of functionality, both PLCs and DCS systems can be used for Automation, SCADA (Supervisory Control And Data Acquisition), MES (Manufacturing Execution Systems), or ERP (Enterprise Resource Planning). However, each system has its own strengths and weaknesses so it’s important to select the right type of system for your specific needs.
Is DDC a SCADA?
DDC is not a SCADA. DDC is an abbreviation for Direct Digital Control. It is a type of process control system that uses digital logic and computers to directly control equipment and processes.
In contrast, SCADA systems use analog or digital inputs to indirectly control equipment and processes.
Conclusion
Yes, PLCs can be used for DDC. Direct digital control (DDC) is the use of digital computers to control the sequence of operations in an industrial process. In a direct digital control system, a computer directly controls the process based on feedback from sensors and actuators.
A programmable logic controller (PLC) is a type of computer that is commonly used in industrial applications. PLCs are ruggedized and designed to withstand harsh environments. They are also programmed using specialized software that allows them to perform complex tasks such as monitoring and controlling processes.